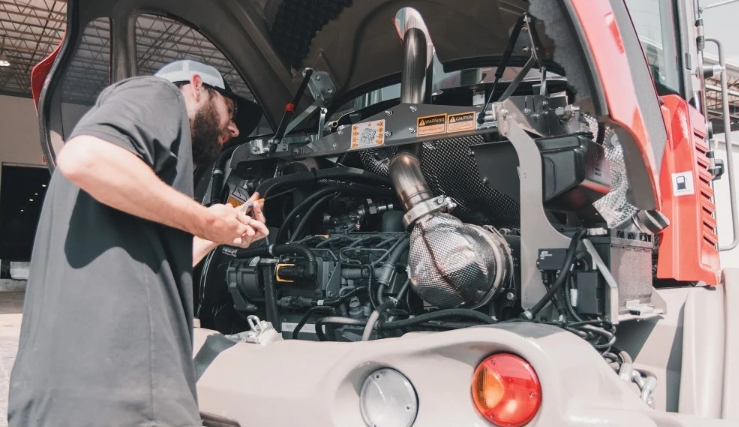
With an expanding array of attachments, compact wheel loaders have become highly valuable for various job site tasks, such as material handling and snow removal. These versatile and robust machines are also relatively easy to maintain. However, adopting a proactive maintenance approach can make all the difference between a productive workday and unexpected repair demands.
According to Lee Padgett, the product manager for Takeuchi-US, taking care of your compact wheel loader should begin as soon as you take possession of your new or used machine. He advises thoroughly reviewing the operator’s manual and adhering to all recommended maintenance practices, including daily checks, as the most effective approach.
Padgett provided a comprehensive guide on how to properly care for a compact wheel loader, along with essential tips to avoid common mistakes.
Wheel loader daily maintenance
Visual checks: Before starting up the machine, do a quick visual check of the CWL and take these precautions:
- Ensure the machine is clear of debris in crucial areas like the radiator, AC condenser, and exhaust. For significant debris buildup, use compressed air or high-pressure water to clean before operating the wheel loader.
- Inspect for any visible oil leaks.
- If applicable, drain the fuel and water separator.
- Examine tire pressure and condition. Look for punctures, gouges, visible metal, or insufficient tread depth, indicating the need for immediate tire replacement.
- Check all vital fluid levels, including engine oil, engine coolant, hydraulic oil, fuel, and windshield washer fluid. Top up if necessary.
- Verify the functionality of all driving and warning lights.
Padgett advised that since not all engine or machine manufacturers provide low-fluid-level warnings, it’s essential to conduct a daily visual check as a good practice. If everything appears to be in order, the next step is to start the greasing process. All pivot points should be greased either before starting or at the end of the shift, based on individual preference.
During the greasing process, it’s crucial not to overlook greasing the articulation point, which is often forgotten. Before greasing the joint, ensure to clean the grease fitting thoroughly. Neglecting this step may cause accumulated dirt on the fitting to be pushed into the pin boss. Consequently, the dirt will contaminate the grease and act like sandpaper between the bushing and pin inside the pin boss, leading to premature wear. Paying attention to these details can significantly extend the lifespan of the equipment.
Operator Safety: Lastly, prioritize checking all aspects related to operator safety. Before entering the cab, operators should clean the mirrors and windows, particularly if they used compressed air or water to remove debris. Once in the operator’s seat, verify that the brakes are fully functional and ensure the backup alarm is operational. These measures help ensure a safe working environment for the operator and those around the machine.
“After completing all these daily checks, operators can begin their work,” Padgett remarked. “With the assurance that the machine is in excellent condition, they can tackle their tasks with peace of mind, knowing it will serve them well and efficiently get the job done.”
Wheel loader weekly maintenance
Perform comprehensive greasing of the machine at the pivot points, bushings, and bearings on a weekly basis, or approximately every 100 hours of operation. Apart from additional greasing, the weekly maintenance tasks demand a more in-depth inspection compared to daily tasks.
Here is a revised version of the maintenance checklist:
- Inspect the electrical connections, cables, and plugs for any issues.
- Clean and securely attach the battery contacts.
- Check for blown fuses or loose connections in the fuse panel.
- If the radiator and oil cooler are dirty, use compressed air or high-pressure water to clean them from the inside out. Be cautious to avoid causing any damage during the cleaning process.
- If required, clean or replace the engine air filter, especially for operators working in dusty environments like demolition or site prep applications. Avoid using high-pressure compressed air to clean the air filter or hitting it against anything to free it from dirt, as this may damage the filter.
- Verify the lug nuts on each tire and tighten them to the appropriate torque.
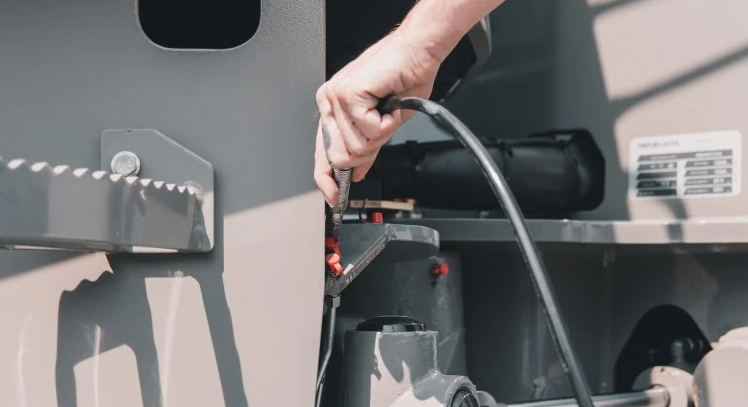
Wheel loader hours-based services
“It’s crucial to log hours when using a CWL for a reason,” Padgett emphasized. “When the machine reaches 250 and 500 hours, there are additional tasks that require attention, so being aware of approaching these milestones is essential.”
At the 250-hour mark, it is advisable to change the engine oil and fuel filters based on the manufacturer’s recommendations. Typically, most engine manufacturers require an initial engine oil change after the break-in period, and subsequently, oil change intervals are generally set at 250 to 500 hours.
Inspect the oil level in the front and rear axles, power divider, and all four planetary drives. It is advisable to perform an initial service for the wheel loader’s planetary assemblies after the first 250 hours of operation.
At the 500-hour mark, change the oil in the front and rear axles, power divider, and all four planetary drives. After the initial 500 hours, subsequent replacements will be required every 1,500 hours. Additionally, remember to replace the axle breathers and inspect battery posts for corrosion, cleaning them if necessary.
Wheel loader annual maintenance
The subsequent significant service intervals occur at 1,500 and 3,000 hours. During these milestones, it is essential to replace the oil in the axles and hydraulic system as it approaches the end of its service life. Additionally, conduct a thorough inspection of the wheel loader to identify and address any loose or worn parts.
At 1,500 hours, as previously mentioned, it is essential to replace the oil in the axles, power divider, and planetary drives. Additionally, remember to change the hydraulic oil and service the brake system during this maintenance interval.
At the 3,000-hour mark, it is crucial to replace the hydraulic oil, air filters, and breathers. Additionally, take the opportunity to verify that all bolts and screws are tightened to the appropriate torque specifications. Inspect the hydraulic hoses for signs of fatigue, cracking, or leaks, and promptly replace any hoses exhibiting these issues. This comprehensive maintenance at the 3,000-hour interval ensures optimal performance and longevity of the compact wheel loader.
Wheel loader engine maintenance
A diesel engine typically requires maintenance at specific hourly intervals, as specified by the manufacturer. This maintenance will involve tasks such as fluid changes, valve-train adjustments, and thorough checks of the fuel and exhaust systems. Following the manufacturer’s guidelines ensures the engine’s reliability and efficient performance.
Padgett emphasized the importance of a crucial operational technique for wheel loaders equipped with turbo engines – the warm-up and cool-down process. It is essential to allow the engine time to warm up before subjecting the machine to a load, and also let it cool down before completely shutting it off. Despite the misconception that the engine’s size makes cold starts and hot shutdowns harmless, they can actually cause harm, so following proper warm-up and cool-down procedures is essential for maintaining the engine’s health.
Continuous idling of a Tier 4 Final engine can lead to regeneration problems. However, taking a few minutes to warm up the engine at the start of your shift and allowing it to cool down at the end can prevent premature turbo failures or engine damage without any significant inconvenience. This simple practice goes a long way in ensuring the engine’s longevity and smooth operation.
Padgett emphasized that engine manufacturers provide their own service and inspection guidelines. Therefore, it is essential to review the engine service manual to gain insights into the best practices for maintaining your engine throughout its lifespan. Following the manufacturer’s recommendations ensures the engine’s optimal performance and durability.
Avoid common mistakes
Compact wheel loaders are highly durable machines that seldom break down if they receive proper maintenance. The majority of failures can be averted through diligent upkeep. According to Padgett, Takeuchi identifies two common issues that can significantly affect a wheel loader’s productivity.
Greasing the machine is crucial for the longevity of wheel loaders due to their numerous articulating and pivoting components. The articulation joint, which constantly moves and experiences significant stress, requires ample grease to prevent premature wear of the pins and bushings. Additionally, the wheel loader’s steering cylinders and loader pivot points should also be greased daily to ensure optimal performance and minimize wear.
Might not be immediately apparent is the presence of multiple operators. Manufacturers often encounter issues arising from different operators using the same machine at various times, with each assuming that someone else has taken care of daily maintenance. This lack of communication and assumption can lead to neglect of essential maintenance tasks, potentially impacting the machine’s performance and longevity. Proper coordination and communication among operators are vital to ensure consistent and diligent maintenance practices.
Padgett illustrates the scenario of a compact wheel loader left at a job site for loading and unloading materials. If one operator finishes their shift and departs, assuming that the next operator will handle greasing and oil checks, or believes the previous operator has already done so, it may result in neglecting these critical tasks for several days. As a consequence, breakdowns can occur due to the lack of essential maintenance, highlighting the importance of consistent and responsible maintenance practices among operators.
“Begin by reading and adhering to the procedures outlined in your operator’s manual; this serves as an excellent foundation. However, fostering open communication with all machine users is equally essential. Implement processes that guarantee your machine receives the necessary attention, and in return, it will serve you effectively for many years.”