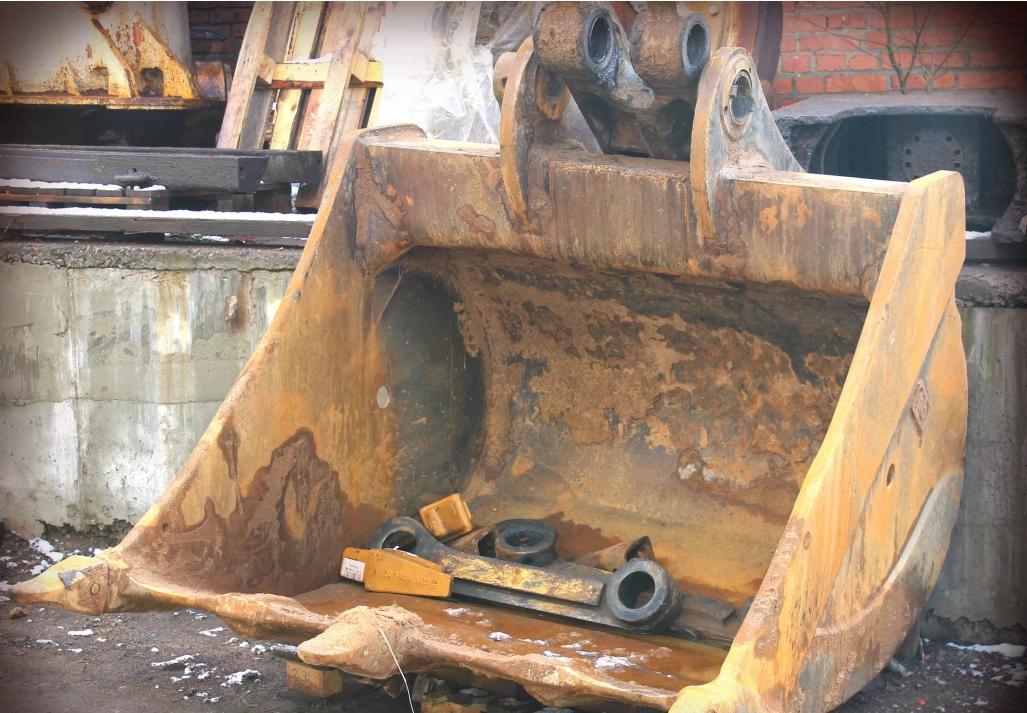
Modern special equipment has a high level of reliability. And if the machine is provided with proper operation, then the excavator will not only successfully fulfill its warranty period, but also maintain its operability as a result of preventive and repair work. But even the most high-tech and technically advanced special equipment can break down.
According to the statistics, it is the rented excavators that break down most often. And this is a consequence of the improper use of this type of special equipment. Excavator rental companies rarely follow the manufacturer’s recommendations for operating the machine. Therefore, in order to maximize the life of this equipment, you need to know about the most important nuances of its correct operation.
A few words about the most frequent breakdowns
Despite the fact that different types of excavators have significant structural differences, a number of the most typical malfunctions can be distinguished for all types of this equipment:
The most common breakdowns in the hydraulic system. Its main parts are the hydraulic pump, hydraulic motor and hydraulic cylinders. The latter provide the maneuverability of the excavator bucket. As a consequence, they are the ones who experience the maximum during the operation of the equipment. The following breakdowns are most common: wear of the piston seal, wear of the inner surface of the liner, violation of the integrity of the thread, a bent stem, as well as the occurrence of a leak in the running sections through the seal elements. If the equipment needs repairs of medium complexity, then worn parts are replaced. In the event of a major overhaul, the cylinder is replaced.
Also, malfunctions often occur in the valves. This problem occurs due to an incorrectly adjusted gas distribution system. In order to prevent valve malfunction, it is necessary to constantly monitor the temperature regime of the valve.
Due to the high load when skewed, breakage of the fingers on the excavator bucket can occur. First, backlash occurs, the result of which is a breakdown. Therefore, when making frequent bucket changes, do not forget to periodically change the fingers.
Cracking and subsequent rupture of the high pressure hose shell. These malfunctions occur when the pressure builds up in the hydraulic system. To prevent this from happening, it is necessary to systematically check the settings of the safety valve. It is also necessary to make sure that the fluid is compatible with the material of the hose. Use only the fluid recommended by the manufacturer. If any physical defects are found in the sleeve, it should be replaced.
Various kinds of mechanical damage. For example, cracked taillights due to reversing, broken glass.
The most serious problems in the operation of such equipment arise when using low-quality fuel. This often results in a major overhaul, since low-quality fuel leads to premature wear of carefully fitted injectors. Subsequently, the injection pump may fail, which will entail repairs with significant financial investments.
Another no less serious problem is malfunctions that occur in the chassis, namely, the breakdown of sprockets, rollers, idler wheels, chains, etc. To prevent breakdowns, timely diagnostics of these systems is necessary. An experienced specialist can assess the degree of wear of these systems “by eye”, but it is still better to use modern diagnostic devices.
Problems arising from improper operation
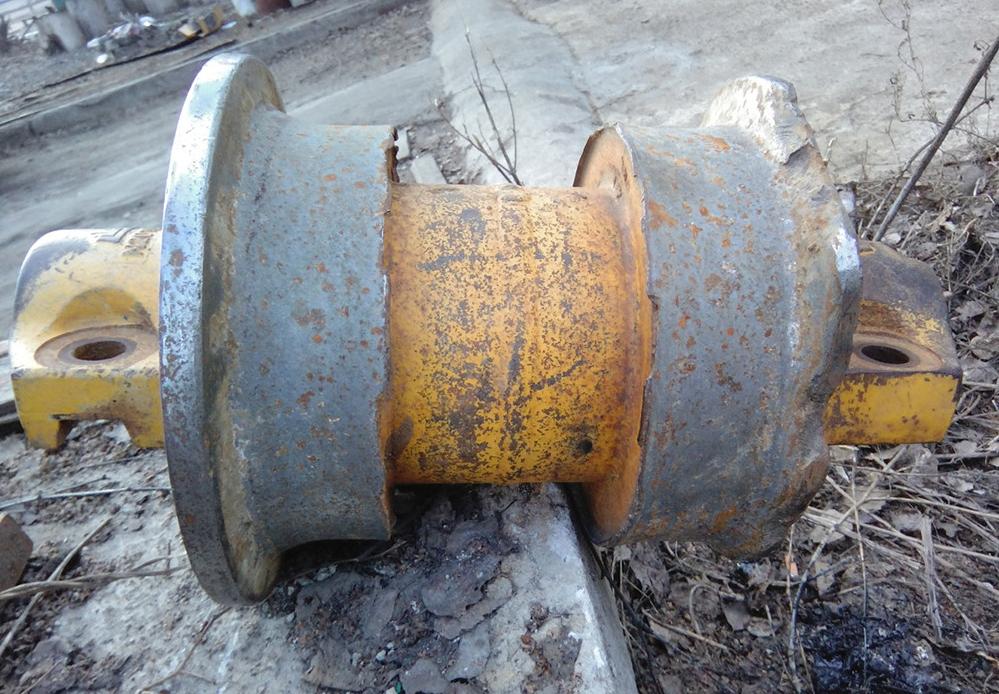
Negligence in battery performance. In an effort to save on fuel, operators often run the engine for short periods of time. This leads to a rapid discharge of the battery, which under operating conditions does not have sufficient time to recharge. Such savings will lead to an early failure of expensive equipment.
When using non-seasonal fuel, breakdowns also occur. So, when working in winter, the use of summer fuel is categorically unacceptable. The fact is that wax crystals, which are in summer fuel, freeze when used in winter, which leads to the formation of plugs in fuel lines and filters. This, in turn, causes the engine to stall. Therefore, it is necessary to use fuel strictly for its intended purpose, and damage can be avoided.